Last Updated on 2021/10/28
Kyushu is one of the most famous ceramics area in Japan
Many famous brands of ceramics (pottery and porcelain.) which have great quality are produced in Kyushu. Those brands are Arita, Imari and Karatsu in Saga, Hasami in Nagasaki, Koishiwara in Fukuoka and Satsuma in Kagoshima. Kyushu is one of the most famous production regions of ceramics in Japan.
Difference between pottery and porcelain
Now, what do you think is the difference between pottery and porcelain? Simply, it is the main material, i.e. pottery is made from clay while porcelain is made from stone (powder).
Porcelain is glassy so it repels water and can be made thin. Pottery is water absorbing so it is relatively harder to dry. Pottery is thick and goes less hot than porcelain. It is attractive that pottery has textured surface which has a feel of made by hand.
Onta-yaki is made by hand at only 10 family-run kilns
Among those ceramics in Kyushu, my favorite is Onta-yaki in Oita. Onta region is deep in the mountains that are 17 km away north from Hita City, Oita prefecture.
They started making pottery about 300 years ago, in 1705. There are 10 kilns now. Each kiln is run by only family members so no outsiders involve in the ceramics production.
This place is known as that the British ceramic artist, Bernard Howell Leach has ever worked.
Onta-yaki is made from mud, stone, timber in the mountains, which are natures in Onta area. Besides, all of them are made by hand.
Its feature is just simple and heartwarming. If you walk around the village of only 10 kilns, you may sometimes hear the sound of mortars crashing the clay with the murmur of a stream. That would excite the emotions of the travelers.
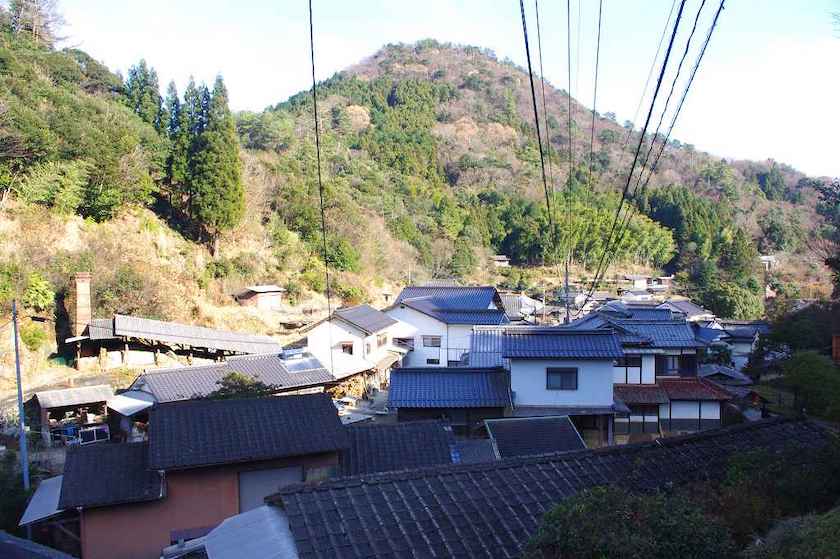
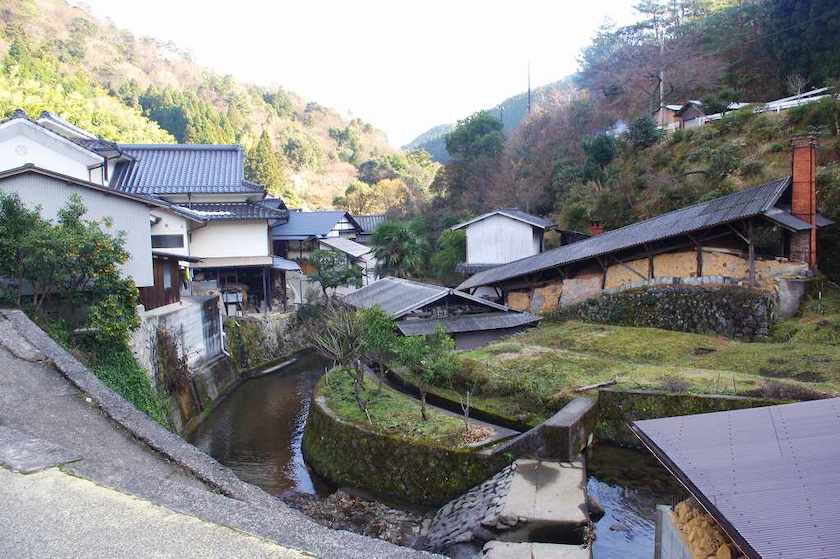
Scenery of Onta. At the present time, this place is really like another world. You can see traditional Japanese scenery here even now.
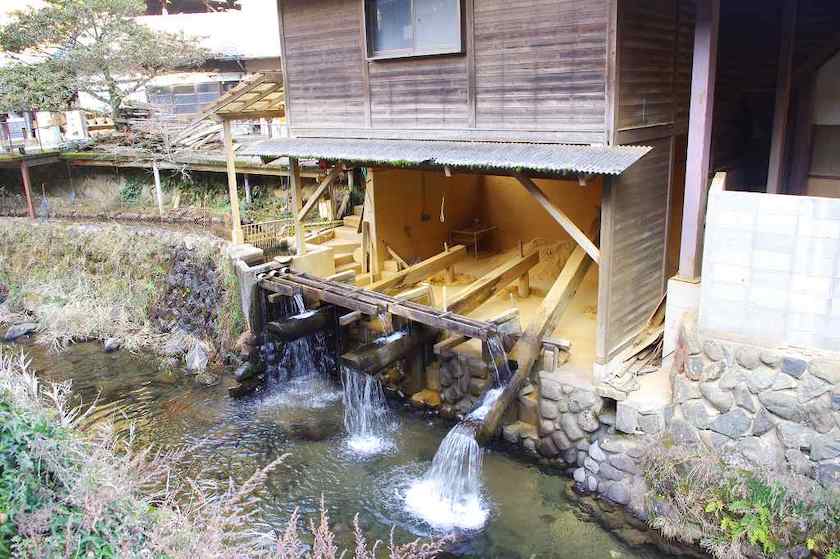
A mortar is crushing the clay of the mountains in Onta with water of the river there.
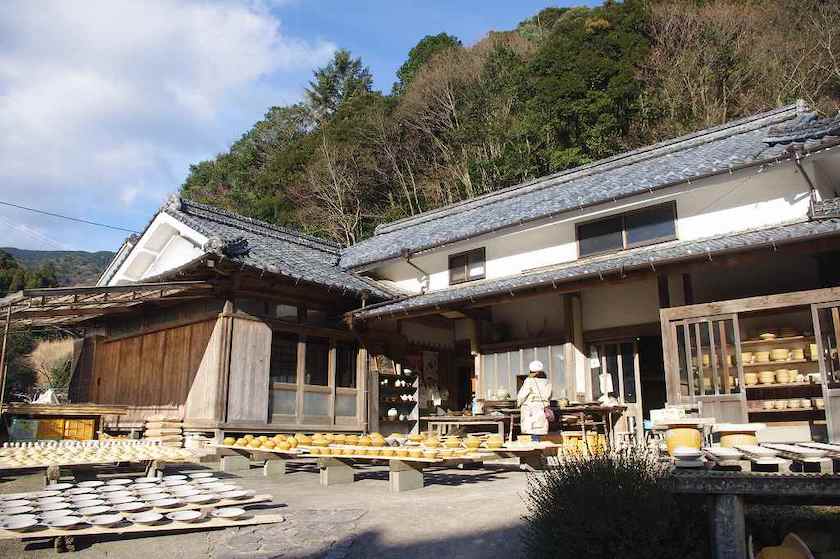
You can buy ceramics of Onta at every kiln.
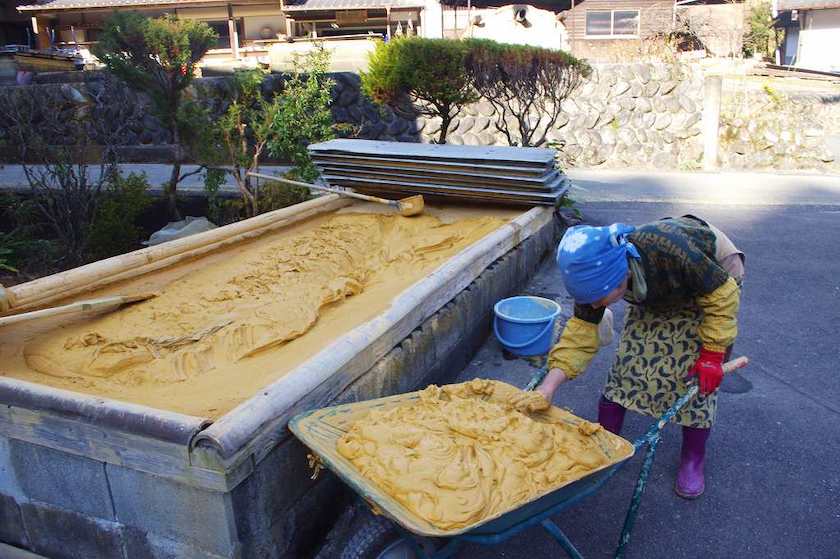
Getting rid of water
Water is removed from the mud after impure substances have been taken out from it in a water tank.
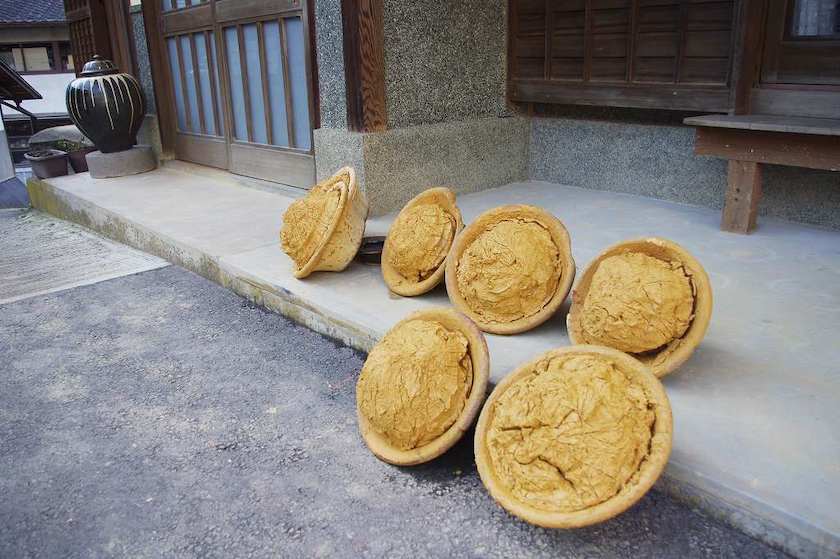
After removing water, mud is put in an unglazed ceramic bowl and dried there. It takes about 20 days.
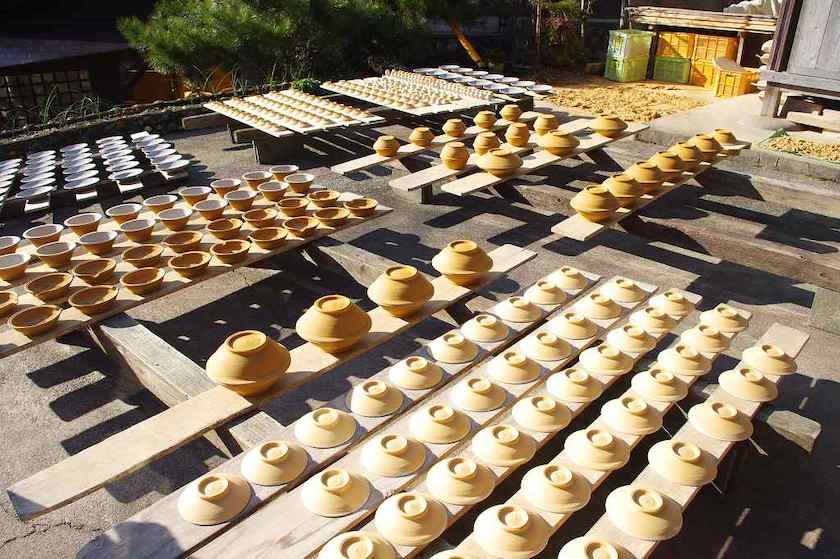
A ceramic shaped with a pottery wheel is dried up in the sun or in shade for about 3 days.
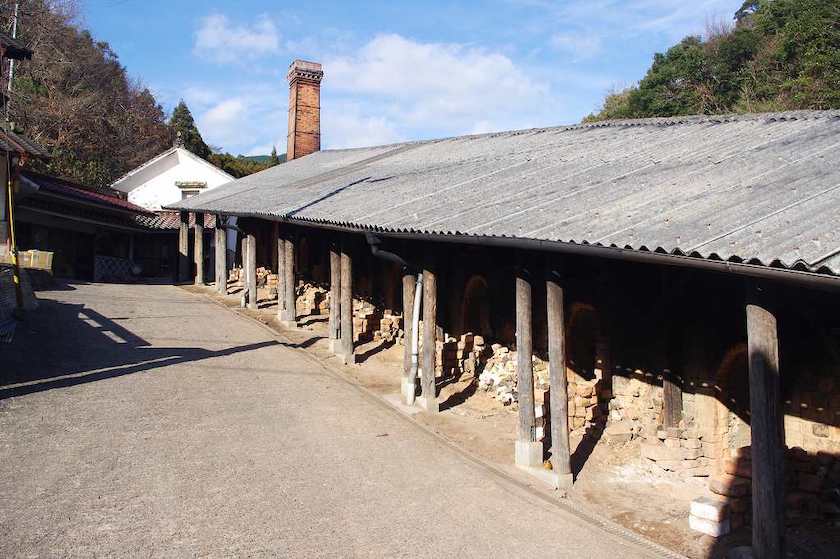
Nobori-gama (a climbing kiln)
A ceramic is baked in Nobori-gama or a climbing kiln for about 60 hours, the fire kept going at any time.
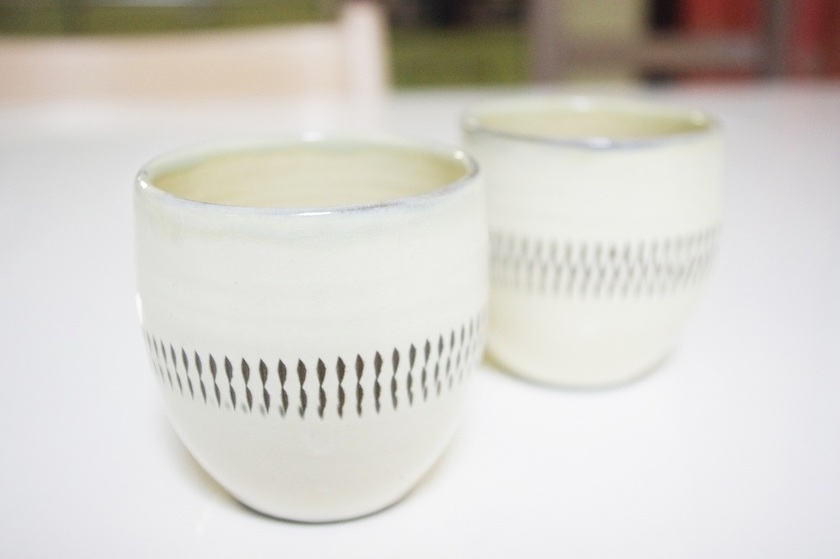
Tobi-kanna
This is my favorite tea cup. Its texture is soft and gives me a wonderful moment.
Among other things, this rhythmic design is the feature of Ontayaki. This design is produced with a tool, tobi-kanna.
If you have any questions, please feel free to contact us by the website form.